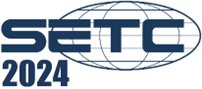
Modeling Transient Control of a Turbogenerator on a Drive Cycle


Modeling Transient Control of a Turbogenerator on a Drive Cycle
GTDI engines are becoming more efficient, whether individually or part of a HEV (Hybrid Electric Vehicle) powertrain. For the latter, this efficiency manifests itself as increase in zero emissions vehicle mileage. An ideal device for energy recovery is a turbogenerator (TG), and, when placed downstream the conventional turbine, it has minimal impact on catalyst light-off and can be used as a bolt-on aftermarket device. A Ricardo WAVE model of a representative GTDI engine was adapted to include a TG (Turbogenerator) and TBV (Turbine Bypass Valve) with the TG in a mechanical turbo-compounding configuration, calibrated using steady state mapping data. This was integrated into a co-simulation environment with a SISO (Single-Input, Single-Output) dynamic controller developed in Simulink® for the actuator control (with BMEP, manifold air pressure and TG pressure ratio as the controlled variables). Transient verification with WAVE-RT was conducted on WLTP and NEDC drive cycles, estimating dynamic energy recovery and fuel consumption improvement. Hints are given for a more advanced MIMO (Multiple-Input, Multiple-Output) control system architecture and calibration.
SAE 2022-01-0415
Presented at the WCX SAE World Congress 2022.
Realis Simulation, formerly Ricardo Software.
Our insights
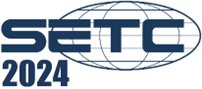
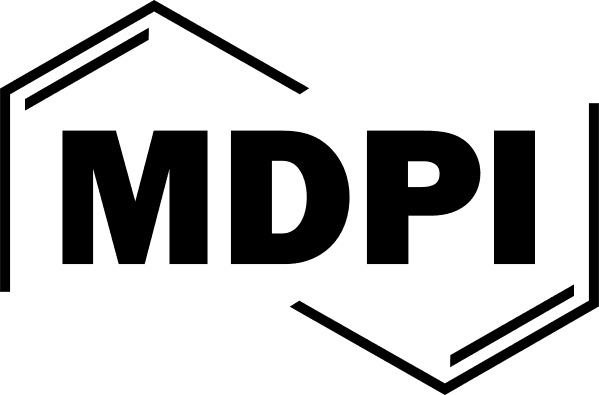
Biofuel Concentration in Low-Speed Pre-Ignition in Gasoline Engines
Technical Paper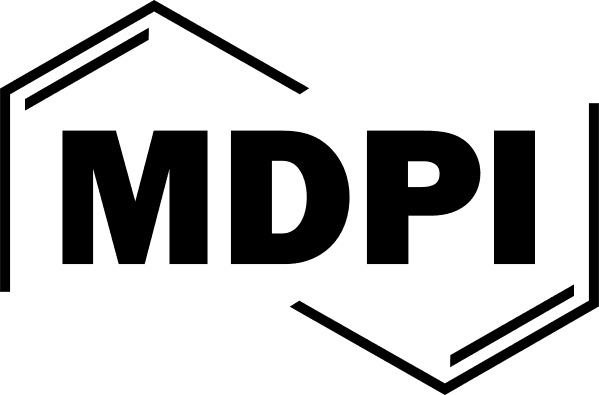