SABR - Gear design

SABR’s transmission assessment capabilities are enhanced by SABR-Gear an integral part of the suite. Users can define initial gear sizes and rate parallel axis gears according to the ISO 6336 standard, including the effect of calculated gear misalignment. This powerful tool enables non-specialists to optimise gear geometry and determine the effect of misalignment on gear life. The designer receives immediate feedback of any change to input parameters both graphically and numerically.
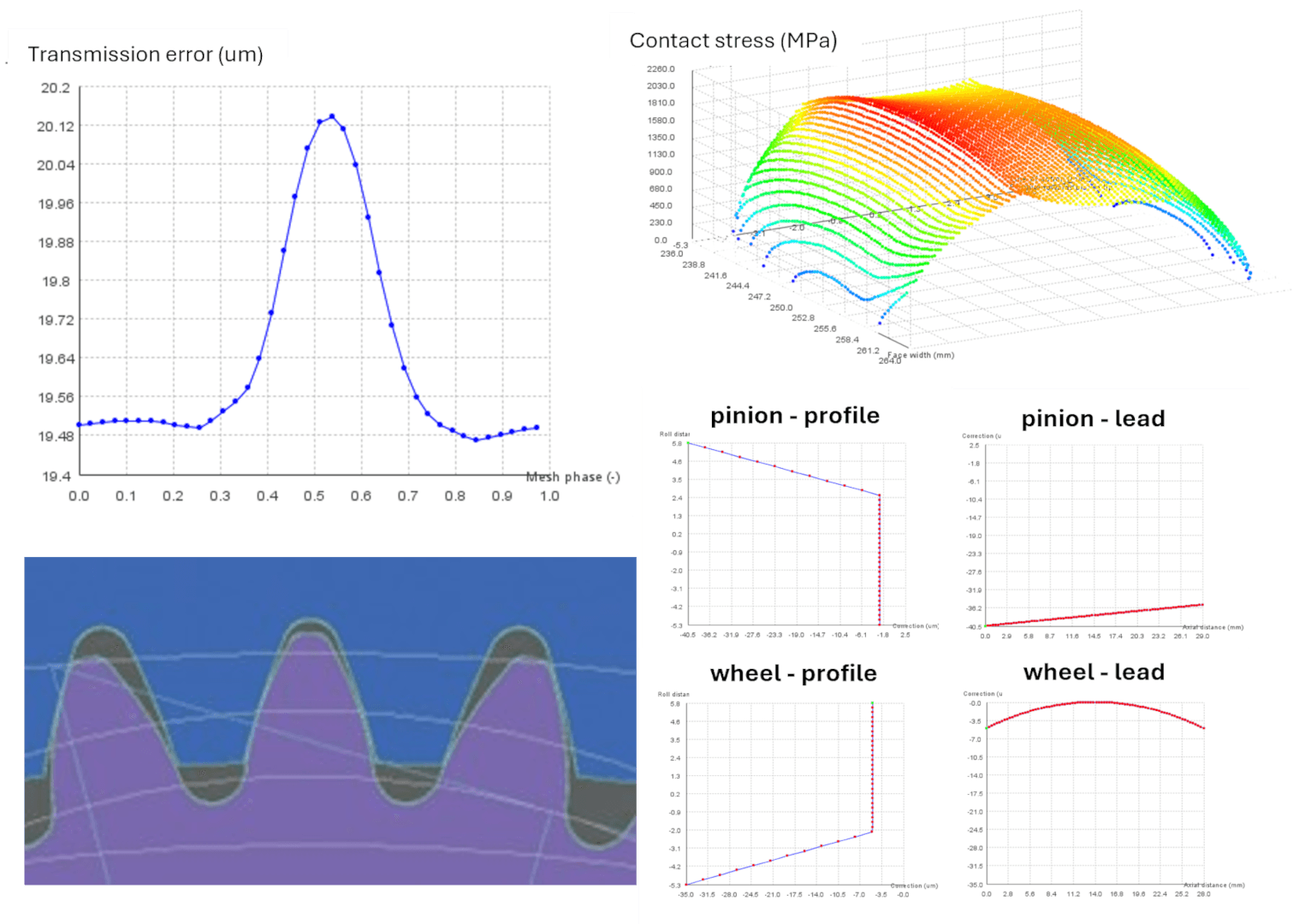
Parameter sweeps can be carried out on multiple input parameters with results filtered to focus on the optimum areas of interest to deliver the highest efficiency gear pair combinations. Tooth Contact Analysis (TCA) considers the effect of micro-geometry and misalignments for all operating conditions, running in seconds where stress, transmission error, flash temperature and oil film thickness are all outputs by default. Transmission error can be exported seamlessly to Realis Simulation VALDYN to perform non-linear time domain Multi-Body System (MBS) analyses of the transmission for NVH assessment.
- Powerful rapid optimiser delivers viable robust geometry designs
- Visual representations of clearances and key design attributes, providing immediate feedback
- Direct import and export interface to SABR, whilst link mode can be used to ensure data is synchronised between the two programs
- Detailed duty cycle function allows multiple loading regimes to be analysed to assess cumulative damage
- Efficiency calculations combining load and speed dependent losses according to ISO 14179
- Parametric sweep function helps to explore the design space more comprehensively and filter on critical design metrics for NVH, durability and efficiency.
- TCA for stress, transmission error, flash temperature and micro-pitting assessment with all duty cycle and misalignments passed from SABR
- Export to GearLab LDP and DONTYNE Load Analysis Model are also available