Case Study - Cold Ambient Warm-up
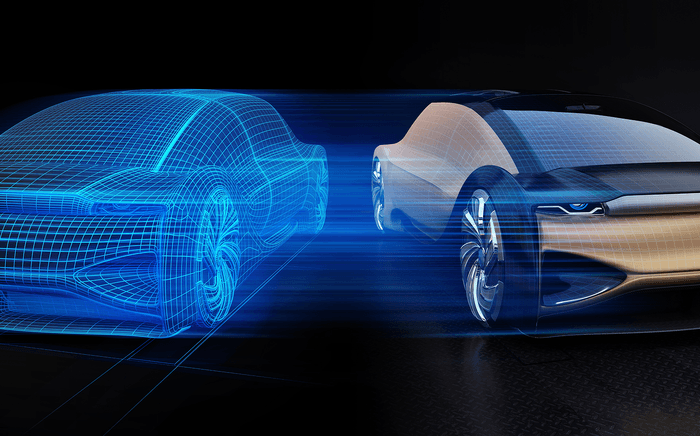
Cold Ambient Warm-up Performance Prediction
Using accurate and integrated 1D modelling methods to achieve results
Using WAVE and Flowmaster, Computational Sciences Experts Group (CSEG) modelled a 2L gasoline turbocharged direct injection engine for the benefit of predicting and quantifying cold ambient heat rejection.
Challenge
A vehicle’s fast and efficient warm-up has a significant impact on occupant comfort, vehicle performance and tail-pipe emissions. Prior to a vehicle being built, thermal systems development teams are consistently challenged with predicting and achieving a vehicle’s ideal ambient start-up performance, especially for cold climate operation.
Difficulties include:
- incomplete knowledge of engine heat rejection and friction
- frequent calibration changes
- the significant costs associated with climate-controlled testing
Validation
Computational 1D models are essential for quantifying the effect of key parameters for engineers to achieve target performance and efficiency. Using this method, an experimental validation test was carried out by CSEG using WAVE, Realis Simulation formerly Ricardo Software’s 1D simulation package, and Flowmaster, the 1D computational Fluid Dynamics (CFD) tool from Mentor Graphics. Initially, using WAVE, a thermodynamic engine model was created and validated for a 2 liter, 4-cylinder gasoline turbocharged direct injection engine with cooled Exhaust Gas Recirculation (EGR.) This model was used to simulate and predict engine heat rejection and quantify the effect of defined calibration parameters such as spark timing, air-fuel ratio, manifold pressure, and cylinder wall temperature in ambient temperature as low as -20 degrees Celsius/ -4 degrees Fahrenheit.
The defined calibration parameters were then applied to a cooling system, developed in Flowmaster where the effects of the engine and coolant thermal inertia and component performance degradation were taken into account to quantity the final effect of various key parameters on cabin air temperature. The combined WAVE-Flowmaster 1D model provided the following analysis and displayed the effects on HVAC performance:
- Spark timing – Time required to reach 50 degrees C was reduced by 110 seconds (23%) for 15-degree crank angle retarded spark timing and 160 seconds (33%) for 25-degree crank angle spark timing. Similarly, coolant temperature increased by 4 and 6 degrees C, respectively.
- Air-fuel ratio – Coolant warm-up was impacted adversely with a richer air-fuel ratio. With richer air flow, the time taken by coolant to reach 50 degrees C was increased by 220 seconds (150%) for AFR-3 and 900 seconds (290%) for AFR-5, when compared to stoichiometric AFR. Similarly, coolant temperature at the end of 10 minutes was reduced by 10 and 20 degrees C, respectively.
- Engine speed – Impact of change in engine speed on coolant warm-up was evaluated by increasing engine speed from 1500 rpm to 1700 rpm. Increased engine speed improved coolant warm-up and the time taken for the coolant to reach 50 degrees C was reduced by 100 seconds (21%) with 1700 rpm.
Opportunity
Using 1D computational models (engine and cooling), CSEG engineers were able to predict engine heat rejection for cold conditions and the effects of engine calibration. This fully computational predictive approach is vital in understanding the complex interactions and mechanics of engine operation at cold ambient warm-up and the levels that HVAC engineers need in order to meet targets in the early stages of design.