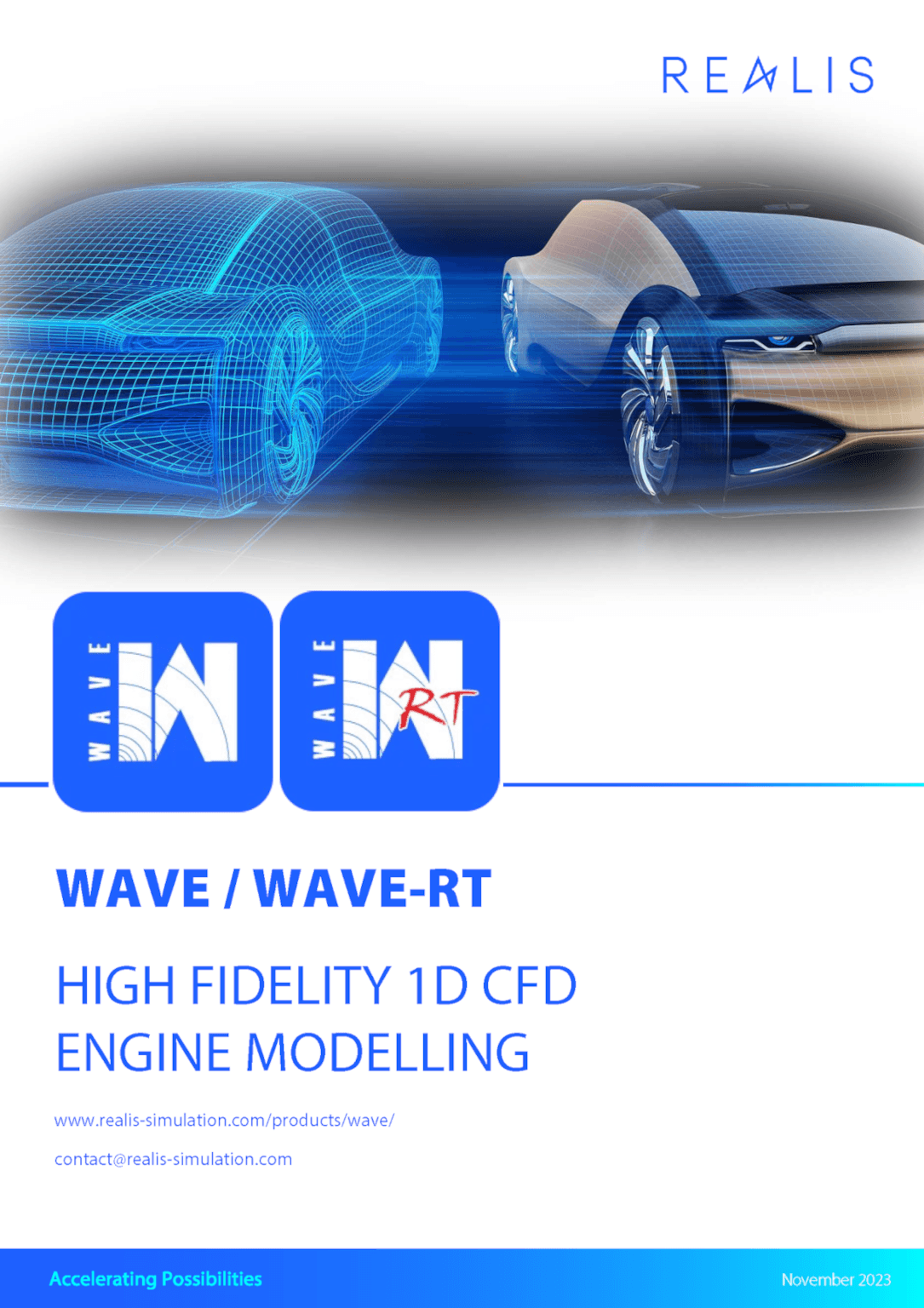
A Simulation Tool for Calculation of Engine Thermal Boundary Conditions


A Simulation Tool for Calculation of Engine Thermal Boundary Conditions
Reducing emissions and the carbon footprint of our society have become imperatives requiring the automotive industry to adapt and develop technologies to strive for a cleaner sustainable transport system and for sustainable economic prosperity. Electrified hybrid electric vehicles (HEV), plug-in hybrid electric vehicles (PHEV) and range extender powertrains provide potential solutions for reducing emissions, but they present challenges in terms of thermal management. A key requirement for meeting these challenges is accurately to predict the thermal loading and temperatures of an internal combustion engine (ICE) quickly under multiple full-load and part-load conditions.
Computational Fluid Dynamics (CFD) and thermal survey database methods are used to derive thermal loading of the engine structure and are well understood but typically only used at full-load conditions. These methods are limited in terms of computational overhead with CFD and the validity of the database when wishing to look at part-load conditions to build up a thermal map of the engine for transient solutions.
This paper presents a new analytical Finite Element (FE) based tool for calculating thermal boundary conditions of all the components of the power cylinder using physical models and semi-empirical correlations, without the need for CFD analysis, and which overcomes the limitation of database methods which are not predictive. An iterative solution is used that captures all the heat paths in detail and where each solution runs quickly enough to allow different design variants to be assessed for multiple operating conditions. The calculated temperatures and the corresponding deformations can then be used to predict piston secondary motion and ring dynamics and to better predict friction, wear and oil consumption of the power cylinder and the structural durability of the components.
The toolset is applied to a 2.0 liter 4-cylinder Gasoline Turbocharged Direct Injection (GTDI) engine and validated with measurements on the piston, cylinder head and cylinder bore for different full and part-load conditions.
SAE 2022-01-0597
Presented at the WCX SAE World Congress 2022.
Realis Simulation, formerly Ricardo Software.
Latest Resources
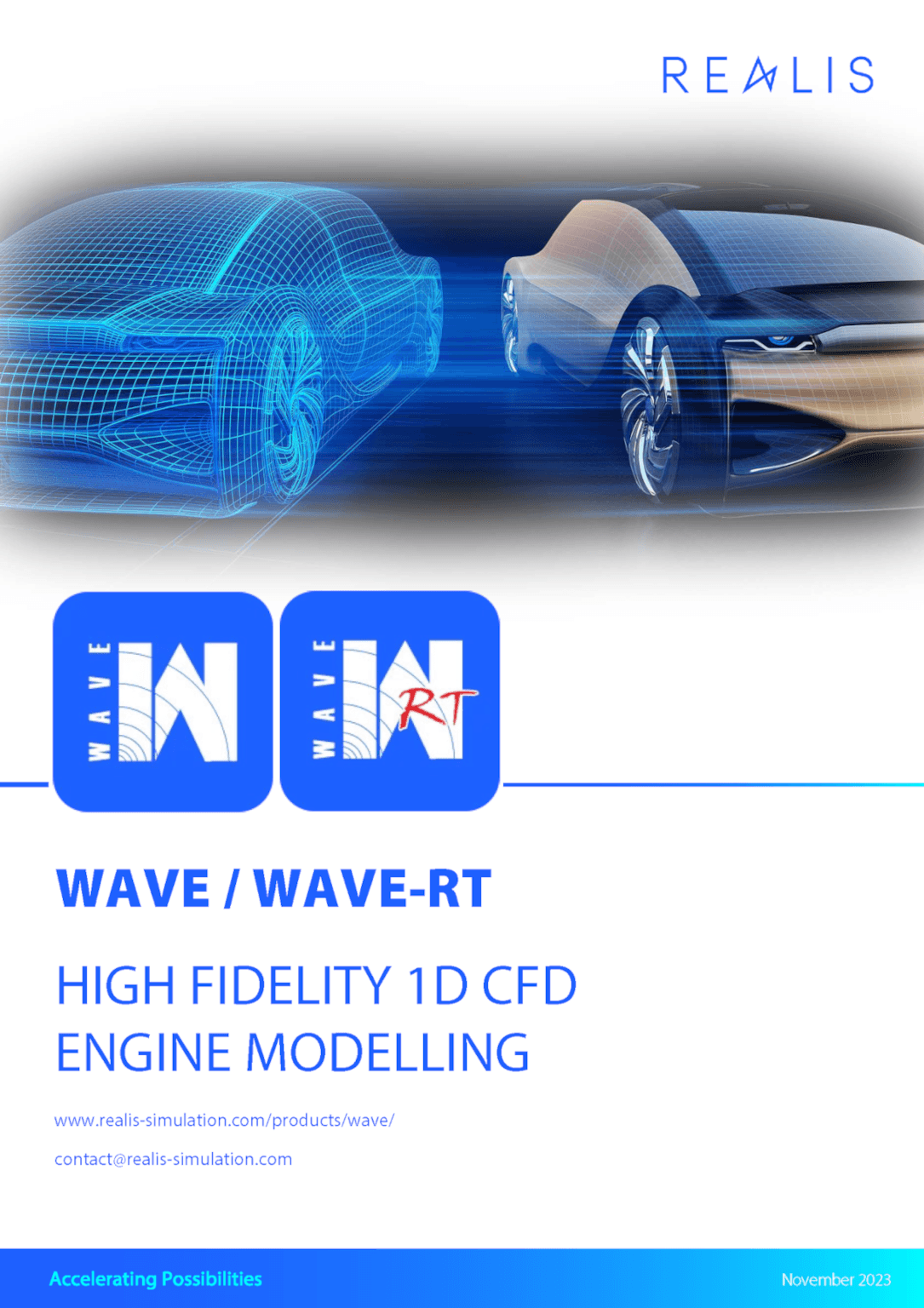

Using Analysis of the Ring Pack and Piston to Optimise Oil Consumption of Current and Future Engines
Technical paper