Case Study - Optimizing drive-cycle waste-heat recovery systems
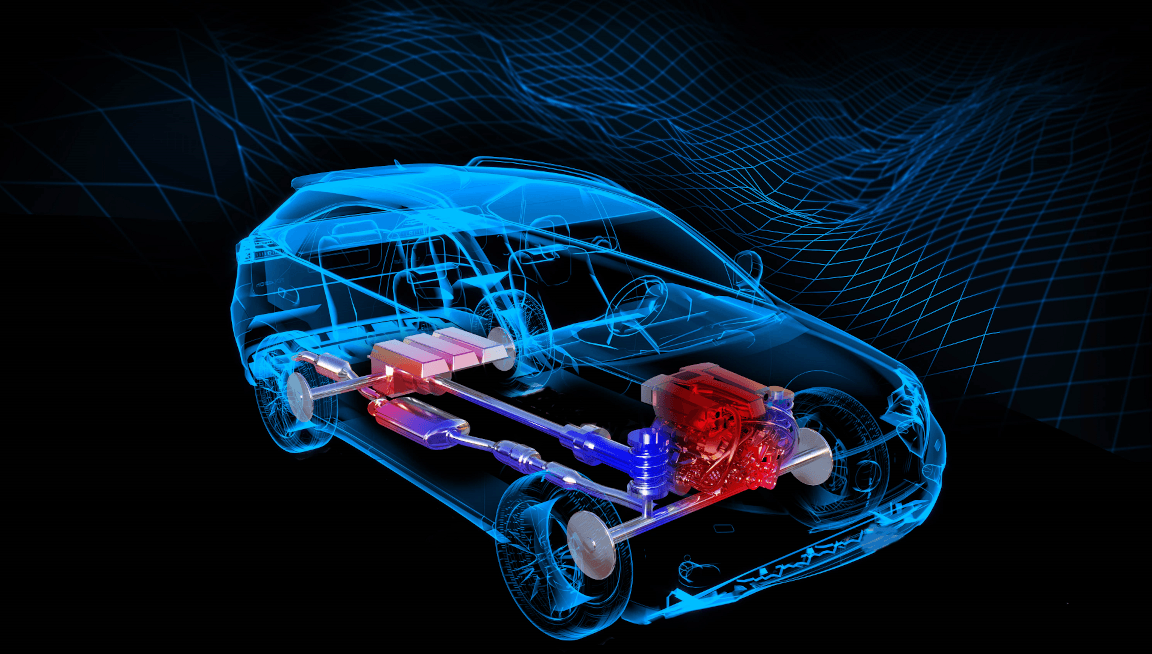
Optimizing drive-cycle waste-heat recovery systems using the Functional Mock-up Interface
Realis Simulation worked in collaboration with Volkswagen AG Research (VWAG) to develop new methods for design and optimization of waste-heat recovery systems in future vehicles.
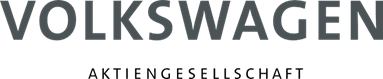
For vehicle manufacturers, there is an opportunity to optimize waste-heat recovery systems for the benefit of recovering exhaust gas and converting it into usable mechanical and electrical energy. This application represents an emerging automotive technology for improving fuel efficiency and reducing CO2 emissions. Successful simulation of waste heat recovery systems requires modelling and capturing the complex interactions between multiple vehicle sub-systems, and as a result often requires the use of multiple CAE software tools. This approach can be cumbersome, costly, inefficient, and error prone. Recognizing the challenge, Volkswagen utilized Realis Simulation formerly Ricardo Software’s model based design CAE software IGNITE to develop new methods for the optimization of waste heat recovery systems in future vehicles.
In order to achieve the level of fidelity and sub-system dynamics required for accurate waste heat recovery system optimization, the functional mock-up interface was used to combine three domain-specific models in IGNITE resulting in a single integrated model.
First, IGNITE was used to construct a full system-level vehicle model needed to confirm boundary conditions and overall vehicle performance. This initial concept level model included a map-based engine model, physics-based plant models of the transmission and driveline, and a longitudinal dynamics capable vehicle. It also included drive-cycle specific vehicle controllers for driver behavior, transmission, shift and engine strategies.
Using the industry standard Functional Mock-up Interface (FMI), engineers rapidly added new and more comprehensive sub-system models including a transient 1D gas dynamics engine; exported from Realis Simulation formerly Ricardo Software’s WAVE-RT toolset using the FMI standard.
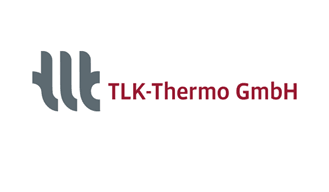
With a transient engine integrated directly within the vehicle model, the next step was to add a detailed waste heat recovery sub-system model. Using TLK-Thermo’s TIL-Suite library, Volkswagen built a physics-based model of an organic Rankine system, which included physical models for the pump, evaporator, and expander and condenser operation. Similar to WAVE-RT, the TLK model was imported, using FMI standards, directly into the IGNITE environment and combined with the engine and vehicle models.
By combining flexible modelling fidelity with the multi-domain integration capabilities of the Functional Mock-Up Interface, IGNITE provided Volkswagen engineers with a flexible and efficient approach to advanced systems simulation and optimization.