ENGDYN - connecting-rod analysis
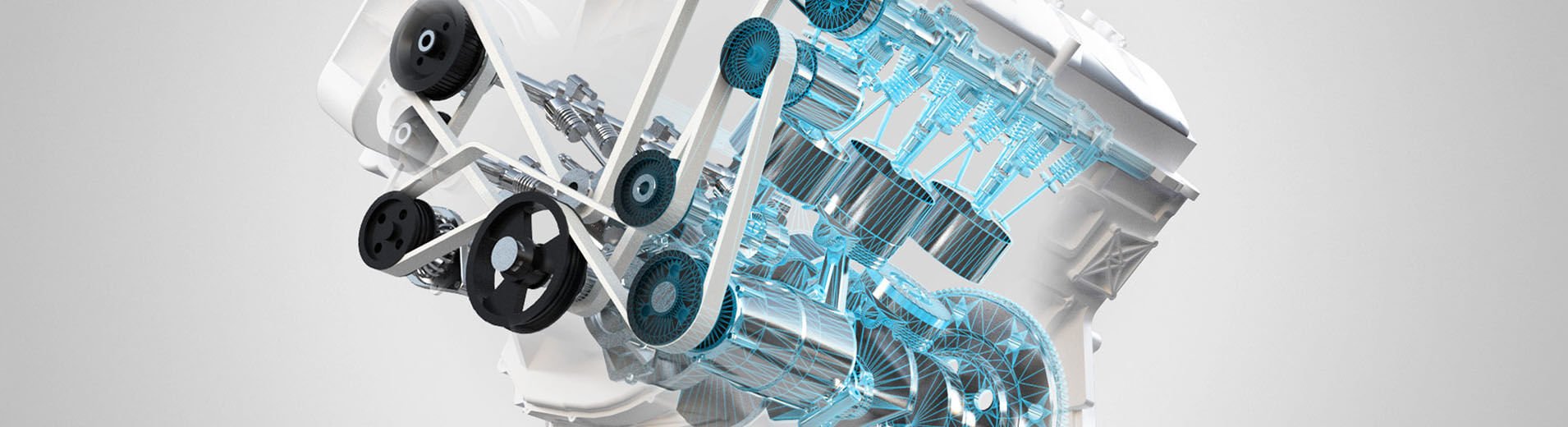
ENGDYN’s simulation capabilities incorporate a range of connecting-rod models from a simplified rigid representation through to fully 3D compliant or dynamic models. By default, ENGDYN simply applies loads to the crank-pin and cylinder assuming primary motion. To consider the dynamic interaction with the crankshaft, and for analysing bearing behaviour due to dynamic loading, ENGDYN can be extended to include a dynamic model of the connecting rod at each cylinder. As with the cylinder-block studies, all required tools to incorporate the 3D models are included in the ENGDYN environment. In addition, the finite element analysis (FEA) interface tool allows users to easily apply the ENGDYN results as boundary conditions for further structural analyses.
Specific connecting-rod applications
- Dynamic interaction between the connecting rod and crankshaft
- Big-end and small-end bearing analysis, including EHL analysis
- Bearing distortion analysis
- Connecting-rod durability
Key features
- Quasi-static and dynamic analysis
- Hierarchy of model types including rigid, compliant and dynamic models, and half models for symmetric rods
- Integrated FEA interface for matrix reduction